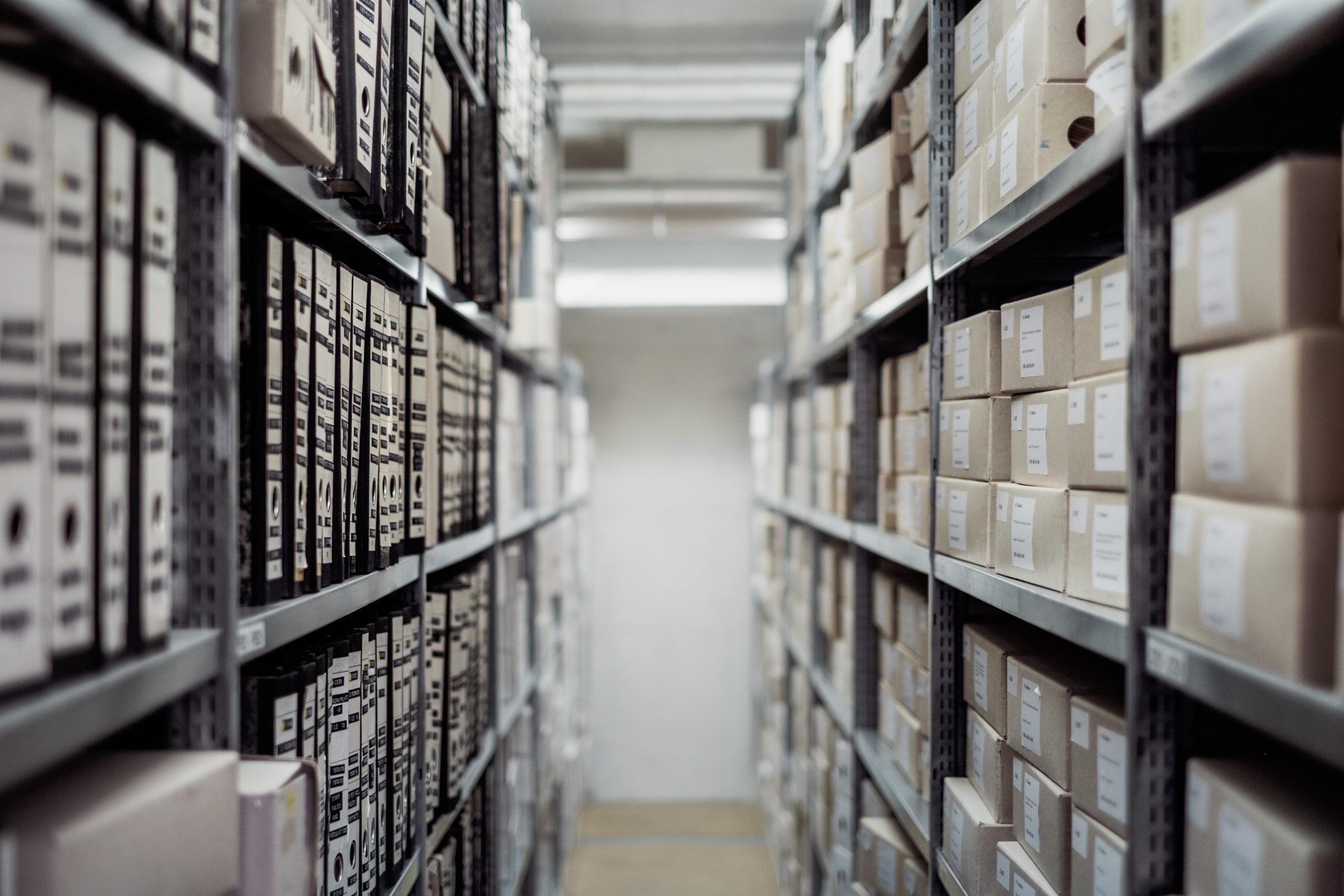
How To Calculate Warehouse Space & Storage Capacity
Photo from Pixabay
Originally Posted On: https://www.smartwarehousing.com/blog/how-to-calculate-warehouse-storage-capacity
If you’ve ever lived with a roommate, you know the unique challenges of arranging a space to accommodate everyone. Whether it was a college dorm or a first apartment, making the proper arrangements to ensure the space is used optimally is an integral part of being able to fit more bodies inside without it becoming chaotic and messy. After all, you want to be able to walk from the kitchen to the bathroom without crawling over furniture, right?
The same principle applies to your warehouse space, but on the greatest scale. By understanding how to calculate your warehouse space and storage capacity, you’ll be able to effectively reduce costs, maximize productivity, and drive profitability and ROI for your organization. Storage space is a hot commodity. When you invest time in optimizing that space, you can increase access to stored goods, accelerating fulfillment and allowing customers to receive their products sooner.
How exactly do you calculate how much warehouse space you have? Here’s a look at how to crunch the numbers and better understand how well you’re utilizing your space.
Calculating the Storage Capacity of Your Warehouse Space
Cost containment and maximizing ROI are two objectives you should aim to achieve when looking for the right warehouse partner. Driving forward momentum across all facets of your supply chain includes identifying how much storage space you need to ensure you aren’t overpaying. When done correctly, you can decrease costs and drive sustainable growth by outsourcing your warehouse needs to a reputable 3PL.
To determine how effectively you’re using your storage space, you must first calculate your total storage capacity. Here’s how:
- Start by calculating the entire square footage of your current warehouse space. For instance, let’s say you’re working with 100,000 square feet.
- Next, subtract the amount of space used for non-storage purposes from your total square footage. These areas should cover any office space, loading areas, bathrooms, break rooms, and similar sections that cannot be used to house goods. (That’s not to say you couldn’t get creative with storing items in offices and bathrooms, but it’s far from ideal.) Let’s use 20,000 square feet as our “non-usable” space. That means your space consists of 80,000 square feet of valuable storage space.
- Now you’ll want to gauge your building’s clear height — in other words, the distance between the floor and an overhead object. Depending on the building, this could mean the expanse between the floor and the facility’s steel shell, or it could encompass the space from the floor to the lowest-hanging object, like a lighting fixture. As you can imagine, the clear height of your warehouse space will affect your total storage capacity because it ultimately governs how high up you can store products.
- From here, multiply the square footage of your usable space (reminder: we’re using 80,000) by the clear height to calculate your total storage capacity in cubic feet. If we use a clear height of 25 feet, the equation will read as follows: 80,000 x 25 = 2,000,000 cubic feet.
We know what you’re thinking: why cubic feet? Measuring the storage capacity of your warehouse space in cubic feet provides you with the framework needed to analyze how effectively you’re using that space. Plus, you can calculate your overall storage utilization in cubic feet to keep numbers aligned and easy to assess.
Am I Utilizing All My Available Warehouse Space?
Now that you know the total storage capacity of your warehouse space, we can drill down further to evaluate how well you’re using that space.
Determine Your Warehouse Space Utilization
Efficiency is key in driving forward momentum for your business. And that includes ensuring you’re optimizing your available warehouse space. By calculating warehousing space utilization, you’ll be able to determine the percentage of usable space you’re currently occupying.
We’re going to let you in on a little-known secret: you should not aim for a perfect 100%. Shocking, we know. The reality is you want to aspire to hit a much lower number. We’ll reveal why after we demonstrate how to measure your warehouse space utilization.
To keep things simple, let’s continue to use the total storage capacity we calculated above, which is 2,000,000 cubic feet. To figure out how much of that space you’re utilizing, you’ll have to determine the inventory cube size of your warehouse space by following these steps:
- Measure the footprints of all the pallet racks.
- Then, calculate their total vertical storage capacity.
- Once complete, multiply the true capacity of each pallet rack by the total number of racks in your warehouse space.
The number you arrive at will ultimately encompass the size of your warehouse space’s storage cube. For instance, let’s say you crunched the numbers and landed on 500,000. If your total storage capacity is 2,000,000, then your utilization of that space equals 25% — and that’s a pretty solid percentage.
Evaluating How Well You’re Utilizing Your Space
So, why is a 25% utilization rate worth a high five? Shouldn’t that number be closer to 100% (i.e. full capacity)? Believe it or not, the simple answer is: No. If your storage utilization is under 22% or over 27% it could indicate a potential problem in the design and layout of your warehouse space.
A percentage above 27% often means your space may be difficult to maneuver. In other words, picking and restocking goods would become a more time-consuming process, resulting in higher labor expenses. Back to our dorm or first apartment analogy: Sure, you could fit the couch between the refrigerator and the bathroom, but it’s inefficient. In the same vein, you could stack products from wall to wall and floor to ceiling. But what you save in storage expense would be spent in inefficiency.
On the opposite end of the spectrum, if you’re below 22%, it’s an indication that you’re potentially failing to leverage the full extent of your valuable space.
Once you have a clear picture of the numbers, you can shift your focus to optimizing your warehouse capacity. Implementing a few small changes to your space can increase utilization and deliver both time and cost-saving benefits.
Maximize Your Storage Capacity
These three tips are designed to help you optimize the storage capacity of your warehouse space.
- Consider What Storage Solutions You’re UsingVarious types of storage solutions are available that can have a positive impact on how effectively you utilize your space. The key is to opt for solutions that complement the shape and layout of the area, along with the products being housed in that space. Some of the more popular storage-enhancing solutions include pallet racks, mezzanines, flow racks, and stacker cranes.
- Strategically Arrange Your SpaceAfter selecting the types of racks, boxes, and storage solutions that best fit your needs, strive to organize your space in the most optimal manner possible. For instance, arrange similarly sized storage units and items together so they fit seamlessly together like puzzle pieces. You can also adjust your aisles, making them slightly narrower to increase the total number of rows you have. Just keep in mind: rows must be able to comfortably accommodate equipment and staff to ensure operational efficiency.
- Take Growth into ConsiderationRemember how outrageous it sounded when we shared that your storage utilization shouldn’t exceed 27%? Well, another reason why it’s important to stay below 27% is to account for new product launches, business growth, and seasonal inventory fluctuations. (You’re planning to grow, after all, aren’t you?) If your warehouse space is at maximum capacity, it’s a pretty strong indication that it’s time to expand.Think about it: what if one of your products gets endorsed by an influencer on social media? Or a write-up on a popular industry website generates millions of views? Your product could potentially go viral overnight. Exciting, right? But if you’re not prepared with the space to handle the influx of orders and meet consumer demand, you’ll risk putting the customer experience — and your company’s reputation — in jeopardy. High demand is a great problem to have, but only if you’re equipped with the space, tools, and technology to properly manage it.
Make Your Warehouse Space Work for You
Finding the right warehouse space for your business can play an integral role in optimizing your supply chain, maximizing revenue, and ensuring a seamless consumer experience. At Smart Warehousing, we have the experience, technology, and national footprint needed to accommodate everything from order fulfillment to inventory management.
By using Smart Warehousing as your dedicated 3PL partner, we can help your business scale and stay ahead of demand. Contact us today to discover how our team can help address key challenges you’re facing and drive long-term growth for your organization.