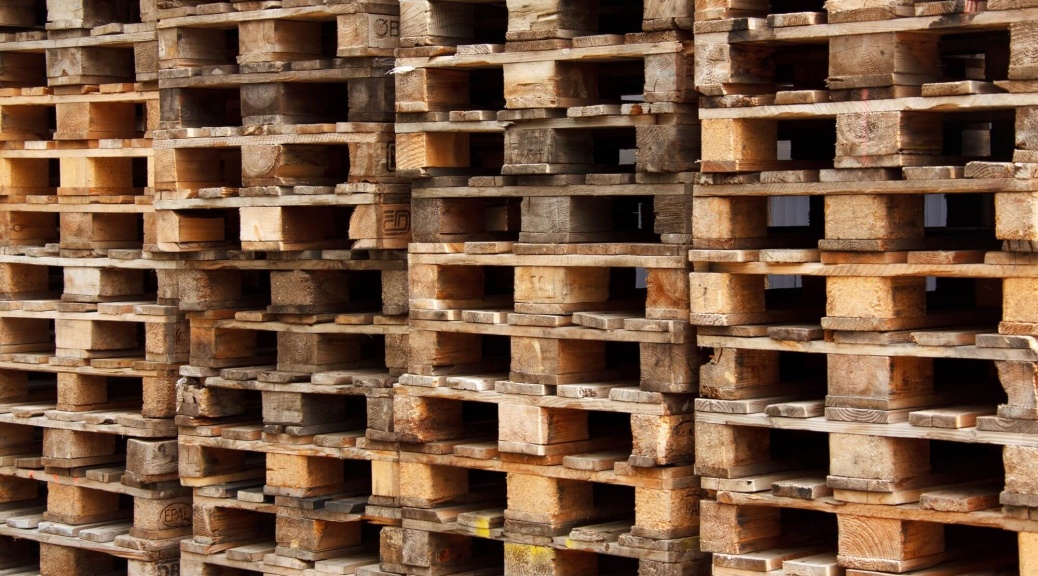
MAXIMIZING WAREHOUSE STORAGE WITH PALLET RACKING SYSTEMS
There are 130 million square feet of warehousing space in the northeast of Florida. This is just a small taste of the amount of warehousing space that’s spread across this southern state.
Each of these warehouses has one thing in common. They need a racking system to keep them productive and organized.
There are several pallet racking systems available, so it’s essential to choose one that will fulfill your company’s needs.
Keep reading to learn what your options are for organizing your warehouse.
Why The Right Pallet Racking System Matters
Choosing the right pallet racking system can mean the difference between an organized and productive warehouse and one that is full of chaos. The organized warehouse will have a significantly better bottom line.
The right pallet racking system will utilize the space in your warehouse in the most effective manner. This will let you store more inventory in the same sized space. This means you can save on the expense of renting out a larger warehouse.
Structural Pallet Racks
Different types of pallet racks will use structural steel to reinforce the channels. This steel is quite thick and creates a strong construction for the storage of your inventory.
Structural pallet racks are more impact resistant and sturdier than roll-formed racking systems.
Roll Form Pallet Racks
Racks that are a roll form style use flat-rolled steel to create the frame of the racks. This type of structure gives the rack its strength and require less steel than a structural pallet rack system.
There’s more variety in the holes you’ll see in this type of build. You could have keyholes, square, or teardrop shapes.
Pallet Flow Racks
You may hear of these racks referred to as gravity flow racks. These racks work best if you need high-density storage for a lot of inventory. Your employees can then pick several different types of inventory from multiple levels at the same time.
The inventory will then have a first-in and first-out (FIFO) cycling. You would load new pallets of inventory onto the backside of the rack at the high end. Then the oldest inventory gets pulled from the lower front side of the racks.
Push Back Racks
This system uses a last-in and first-out system for inventory. This is another system that works well for high-density storage. You’ll be able to access specific products easier with this method.
A rail or roll system is used to keep the pallets in line. When you load a new pallet on the structure, the already loaded pallets move backward on the rails. As you remove pallets from the front, the pallets in the back push forward.
Drive-In Racks
This racking system uses a last-in and first-out system. This system works well in a warehouse where you have limited space. This is because it needs fewer aisles than other systems to give you the same amount of storage space.
The racks are sized so that you can drive a forklift through the aisles. Stocking and arranging additional pallets becomes easier.
Carton Flow Racks
This is a pallet racking system that uses FIFO to manage your inventory. Gravity causes your products to move from the back of the rack to the front of the rack. There are rollers on the rack to make the movement easier.
This is a similar system to the pallet flow racks. Instead of moving the entire pallets, they move individual boxes.
Cantilever Racks
These racks feature vertical spines that several horizontal arms come off of. This gives you several levels of racks to store long materials like wood beams, plywood sheets, or metal pipes.
You can adjust the height and depth of the horizontal arms. This lets you store a wide variety of materials and have easy access to all of them.
Selective Pallet Racks
This is one of the most commonly used racking systems. This is because you can have direct access to each of the pallets and can configure the system to almost any size you want.
This is also the most easily installed system. This makes it easy to change and reconfigure as your pallet sizes change.
Specialty Racking Systems
If you have a specific type of inventory, then there are racking systems designed to cater to the unique needs of your inventory.
- Tires
- Wire
- Wine barrels
- Beer kegs
These racking systems take into account the shape of the inventory to create a racking system for the systematic flow of inventory. They also take into account the unique needs of the inventory. For example, tire racking systems tend to be shorter to follow high pile permits and fire suppression concerns.
Narrow Aisle Racks
By converting to a narrow aisle system, you can increase your yield by 45-50%. This type of system can add storage space to your warehouse without having to physically move to a larger space. This is done by utilizing your unused aisle space.
You will also need to replace your antiquated forklifts to smaller and more agile models that can maneuver in the new narrow aisles.
Compare Pallet Racking Systems
Now that you have a good idea of your options, it’s time to compare the different types of pallet racking systems. Consider the size of your warehouse and your inventory needs.
Then choose the system that will work the best for your business. Once installed, periodically evaluate your warehouse and racking system. Make sure that it’s still the best system for your business.
Contact us today, and let’s work together to create the most pallet racking system for your warehouse.